From the very beginning of the space satellite industry, most of the spacecraft rely on the use of photovoltaic solar energy as the main power supply: to run the sensors, to active heating, to telemetry, to the cooling system, etc. and even in some cases to propulsion the spacecraft.
Silicon solar cells have proved to be suitable for use in space applications, despite their own limitations. Silicon cells have generally lower efficiencies and significant radiation damage than others new materials.
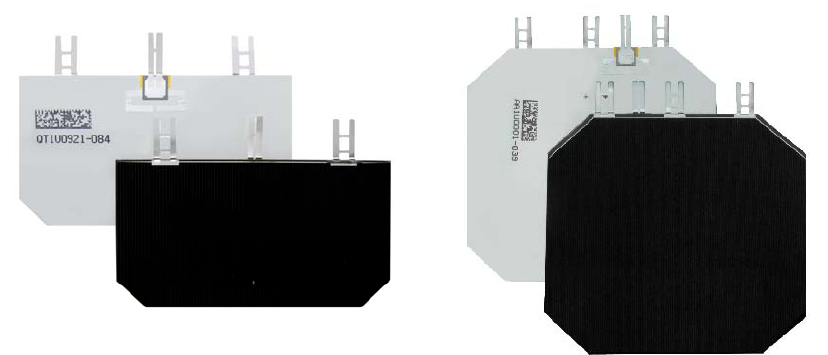
Triple-junction III-V GaAs cells of different sizes.
The new century brought to the space a new type of solar cells with higher efficiencies and better resistance to radiation damage such as those based on the III-V single-junction GaAs. This new material opened the possibility of further improvement by the development of the multiple-junction technologies.
The triple junction technology, where GaInP/GaAs/Ge layers are grown on a Germanium substrate, is giving efficiencies around 30%. Currently, this is the most standard cell structure uses to space applications. The most advance cell structures with 4, 5 or 6 junction cells are reaching efficiencies above 40%.
Solar panels are required to have more output power and less weight and volume, namely, higher specific power and lower stowage volume. To meet these requirements, the simultaneous achievement of both efficiency improvement and weight reduction for solar cells is necessary.
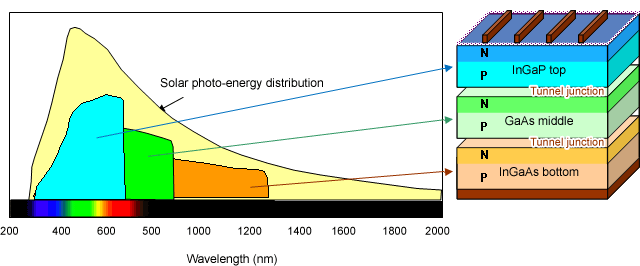
Multi-junction III-V GaAs: Better use of solar spectrum and structure.
But R&D efforts are not only focus on III-V materials. Some important research groups are working with new materials like hybrid perovskites. Perovskites solar cells have the potential to become a disruptive technology in space applications, thanks to the unique combination of appealing intrinsic properties (e.g. record high specific power, tuneable absorption window) and processing possibilities. CdTe solar cells are also a novel development of an affordable thin film cell for space use, which promises an alternative path to the higher manufacturing cost of III-V solar cell. The main potential benefit of this technology is the high-power, in combination with low-weight and flexible thin film.
The most important characteristics that photovoltaic panels must fulfil for space applications are:
- High specific power (W / kg).
- Reduced volume of folding (High power per unit volume W / m3).
- High reliability. The success rate must be 100 % since there is no possibility of repair once the mission is in flight.
- Panels capable of working in conditions of extreme temperatures.
Efficiency of solar array must be known at the Beginning of Life of the system (BOL: Beginning Of Life) but also at the End Of Life (EOL: End Of Life). The power generated at EOL is affected by the following factors:
- Radiation damage: Loss of BOL power per m2 and after a dose of electrons.
- Losses due to temperature correction.
- Losses of BOL power due to UV degradation.
- Micrometeorites (random failures).
- Surface contamination.
Thus, performance must be calculated considering the different parameters correlated to expected losses and random failures that might occur.
The reliability of photovoltaic devices is also a key factor in space application. For this reason, “on ground” life testing of flight representative test devices under “in orbit” representative conditions are essential. Therefore, reliability test plays a key role in the space solar design of the present and future technologies. For standard space solar panels is required the application of standards procedure for the qualification, procurement, storage and delivery for the different space missions.
The standard by which space activity is regulated in Europe was developed in 1993 by ECSS (European Cooperation for Space Standardization). Among others, the standards that apply to photovoltaic products are:
Photovoltaic assemblies and components: This Standard outlines the requirements for the qualification, procurement, storage and delivery of the main assemblies and components of the space solar array electrical layout: photovoltaic assemblies, solar cell assemblies, bare solar cells, cover glass and protection diodes.
This standard does not contemplate:
- The specific requirements for a particular mission.
- Other non-silicon or multi-union cells of GaAs.
- Thin layer cells.
- Concentration photovoltaic technology.
- The acceptance of the module, associations of modules, the photovoltaic subsystem, the structure or the mechanisms of the photovoltaic system.
Testing: This standard addresses the requirements for performing verification by testing of space segment elements and space segment equipment on ground prior to launch. This document is applicable for tests performed on qualification models, flight models (tested at acceptance level) and proto-flight models.
This Standard establishes the basic rules and general principles applicable to the electrical, electronic, electromagnetic, microwave and engineering processes. It specifies the tasks of these engineering processes and the basic performance and design requirements in each discipline.
Other organizations with specific standard for Space Solar Panels are:
American Institute of Aeronautics (AIAA)
- AIAA S-111 – Qualification and Quality Requirements for Space-Qualified Solar Cells.
- AIAA S-112A – Qualification and Quality Requirements for Electrical Components on Space Solar Panel.
International Organization for Standardization
- ISO-11221 – Space systems – Space solar panels – Spacecraft charging induced electrostatic discharge test methods.
The main reliability tests for photovoltaic assemblies and components are detailed in ECSS-E-ST-20-08C. The table is showed some of the test required for a qualification test plan for bare solar cells. Each test is detailed in the corresponding method.
ECSS-E-ST-20-08C
wdt_ID | Test | Method |
---|---|---|
1 | Visual Inspection | 7.5.1 |
2 | Dimension & Weight | 7.5.2 |
3 | Flatness | 7.5.19 |
4 | Surface Finish | 7.5.11 |
5 | Contact Thickness | 7.5.10 |
6 | Solar Cell Reverse Bias | 7.5.16 |
7 | Electrical Performance | 7.3.2.2 |
8 | Hemispherical Reflectance | 7.5.6.2 |
9 | Coating adherence | 7.5.8 |
10 | Humidity & Temperature, and pull | 7.5.7.2 |
Test | Method |
Two of the most significant Alter Technology solar array space reliability tests are described below:
Particle Radiation Effect on Solar Cell Performance
This test is an accelerated life test to quantify the solar cell and solar cell assembly performance degradation due to particle irradiation. Radiation degrades Space solar cells and generates device perturbations that could lead to its malfunction or even destruction.
Particle radiation produces Space solar cells the following effects:
- Ionization may affect cover glass performance.
- Generation of solar cell point defects (i.e. additional recombination centres, diffusion lengths decrease).
The mission particle radiation environment, mainly composed by electrons and protons, is converted into 1MeV electron equivalent fluence.
Bare solar cells or solar cell assemblies are submitted to 1 MeV electron fluence, typically using Van-der-Graff electron accelerators, at a typical rate equal or lower than 5 × 1011 e‐ cm‐2 s‐1. (e.g. the solar cell damage after 15 years in geostationary orbit (GEO) is simulated with around 30 minutes of electron exposure). The exposure is performed at ambient temperature, but for high temperature missions (i.e. close to the sun) and low temperature missions (i.e. deep space) the electron exposure at these extreme temperatures may be also considered.
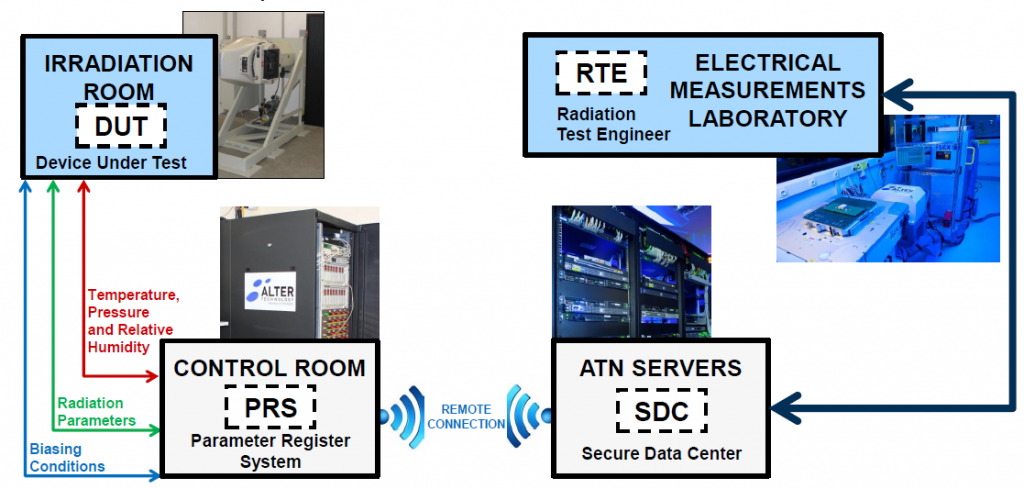
Alter Technology setup during Radiation test. Alter Technology is a recognized Centre of Excellence for ESA and DLA for radiation testing (DLA- MIL Laboratory Suitability and ISO/IEC 17025 certified).
Alter Technology has accumulated significant experience, conducting more than 1000 radiation test campaigns over more than 27 years for ESA projects, and commercial Space Programmes for Space agencies worldwide.
Solar Cell Assembly Environmental Test
The solar cell assembly performance stability is verified under worst case operation conditions for the mission duration with the required margin.
Two methods can be followed for the definition of the life test:
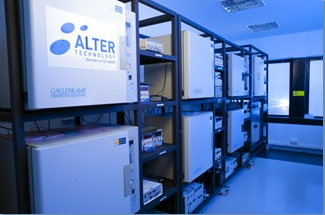
Environmental Test Alter capabilities: Burn-in, life test, Hast among others
- Determine the activation energy, for a failure mode, by measuring the time to failure at several temperatures. These temperatures shall be within the failure mode identified and not exceeding the maximum space mission temperature, to avoid triggering of other solar cell failure modes.
- Demonstrate by assuming an activation energy that the stability is not affected within the duration of the mission.
Performing an environmental test means subjecting the solar cell panel array to certain environmental conditions (cold, dry heat, relative humidity, etc.) in order to check if the electrical and operational parameters remain within the range defined by the applicable regulations.
Alter Technology offers their expertise in testing in a wide range of environmental testing conditions:
- Cold
- Dry heat
- Damp heat (steady state and cyclic)
- Change of temperature
- Composite temperature/humidity test
- Vibration
- Vibration + Temperature
- Impact
- Solar radiation
Alter Technology has an ENAC accreditation to perform Environmental (climatic/mechanical) testing. Our laboratory is a notified body for the EMC Directive 2004/108/EC. It is recognized by NIST (USA) and RRA (South Korea) for EMC testing and is a Recognized Testing Authority (RTA) by the Australian National Association of Testing Authorities (NATA) for EMC and Safety testing.
Procurement Management for Space Solar Cell Arrays
Our commercial and technical expertise and experience allows us to recommend, select and supply Bare Space Solar Cells and all the EEE components on Space Solar Panel Arrays from good manufacturing sources. All parts procured by us are fully inspected and tested to ensure they meet the requirements of the project/customer contract. This enables us to confirm compliance to the:
- Quality and reliability requirements
- Cost constraints/budget
- Delivery schedule
Selection and procurement of the correct Space Solar Cell is essential to meeting the hostile environmental, mechanical and radiation environments encountered in the space industry. To achieve this requires a high degree of engineering expertise and in other disciplines covering a wide range of components and technologies.
- SOLAR CELLS - 30th July 2018
- Radiographic Inspection 3D X Ray – 2D | Hi Rel Electronics Parts - 20th January 2016
- Substrate Attach Strength – Die Shear Strength | EEE Parts - 9th December 2015