Corrosión / Contaminación
Los conectores prensados son uniones herméticas a los gases, idealmente protegidas contra contaminantes ambientales y agentes corrosivos. Sin embargo, el engarce inadecuado y los defectos inherentes del conector y del cable reducen esta protección. Por lo tanto, dependiendo de la atmósfera de almacenamiento, pueden formarse productos de corrosión no conductores, o eventualmente puede inducirse el agrietamiento por corrosión bajo tensión. Los primeros actúan como capa de insolación que reduce la conductividad del conector y ambos efectos de corrosión se identifican como factores críticos involucrados en fallas comunes reportadas para conectores eléctricos. De manera similar, la contaminación orgánica de la superficie en la interfaz de contacto que forma y el aislamiento o la capa de baja resistencia también pueden afectar el rendimiento del sistema.
La Corrosión por Arrastre es la relacionada con defectos en placas y debajo del revestimiento que exponen el metal base (aleaciones de Cu o Cu) al oxígeno u otros agentes corrosivos. Típicos bloques de subplato de Ni por corrosión iniciada por poros. Sin embargo, cuando llega a la base, los productos de corrosión pueden migrar hacia la superficie, lo que reduce la conductividad del contacto en gran medida como se ilustra en la figura.
La Corrosión Galvánica es un proceso de corrosión mediante el cual la presencia de un electrolito (por ejemplo, humedad) en la interfaz de dos metales o aleaciones con un potencial de electrodo diferente promueve la corrosión acelerada del que tiene un potencial de electrodo más negativo (ánodo). En el caso de conectores engarzados, tales celdas galvánicas pueden formarse entre los cables y el cilindro (selección inadecuada del cable y del cilindro); o entre el material de la base del conductor y el recubrimiento protector contra la corrosión (revestimiento dañado). Un ejemplo típico de un par de trenzas de base susceptibles a la corrosión galvánica son Cu y Ag, que son responsables de la denominada “plaga roja”.
La figura muestra, un ejemplo de cable de Ag-Cu afectado por la plaga roja. Teniendo en cuenta la carga aplicada durante los procesos de engarce, las terminaciones de Ag-Cu no se recomiendan para conectores engarzados, a menos que se tomen medidas adicionales para prevenir el desarrollo de la plaga roja (es decir, un grosor de recubrimiento más pesado, un conector con clasificación ambiental, un recubrimiento conforme, un manguito retráctil, etc.)
La Corrosión por Fricción, que también se denomina oxidación por fricción, se refiere al mecanismo de corrosión debido al desgaste que experimenta la interfaz de contacto debido al movimiento relativo de alta frecuencia (vibración). Esto conduce a la rotura de la interfaz de contacto. Los residuos resultantes se oxidan y se acumulan en la interfaz de contacto, dando como resultado la formación de una capa aislante gruesa.
En el caso de conectores engarzados, la corrosión por fricción está relacionada con aquellas situaciones en las que el conector está ligeramente flojo (por ejemplo, debido a una vibración intensa). Esto es más probable para conectores basados en Cu debido a la alta ductilidad inherente.
Los Residuos Orgánicos pueden estar presentes en la interfaz de contacto debido a varias razones, entre ellas el engarce y / o la limpieza incorrectos. Además, pueden ser liberados térmicamente de los materiales plásticos circundantes como el aislante de alambre. Dichos procesos de desgasificación son inducidos por un calentamiento anormal del cable, generalmente relacionado con los eventos electrotérmicos descritos en la siguiente sección.
Herramientas de diagnóstico: los productos de corrosión se pueden detectar mediante diferentes enfoques, a simple vista y con inspección óptica externa de gran aumento. Sin embargo, debido a la estrecha estructura de los conectores prensados, se requieren técnicas de microsección para evaluar la presencia de señales de corrosión en la interfaz de contacto.
Además, las técnicas analíticas capaces de determinar el estado de oxidación (por ejemplo, espectroscopia de fotoemisión de rayos X) y las herramientas de microanálisis que combinan las capacidades analíticas y de imagen (por ejemplo, espectroscopia de rayos X de dispersión de energía) son esenciales para un análisis exitoso de fallas.
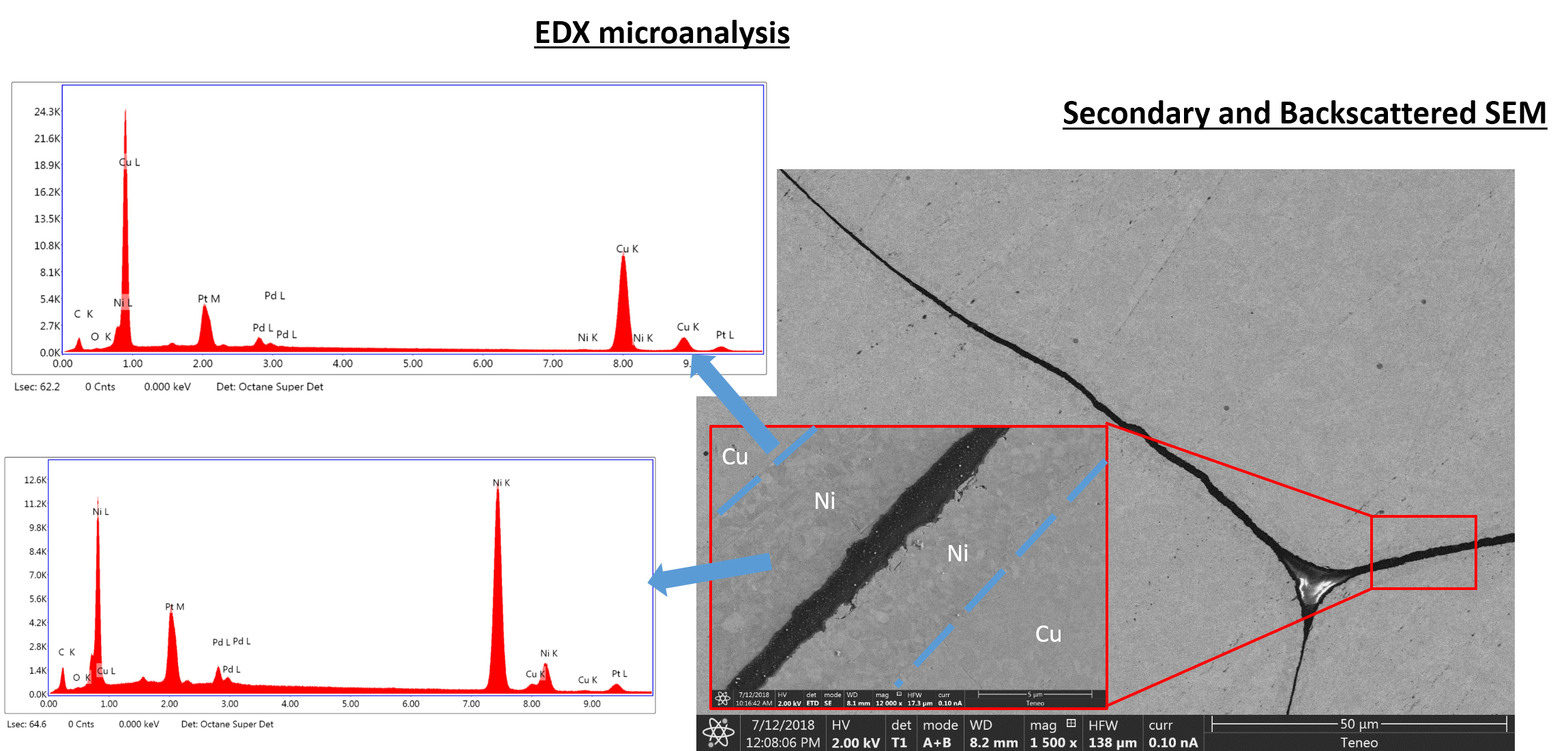
Ejemplo de microanálisis de microscopía electrónica realizado por nuestro laboratorio.
Los fallos en los conectores prensados pueden estar relacionadas con diferentes causas, algunas de las cuales se analizan en otro lugar. El presente post analiza aquellos relacionados con fenómenos de corrosión y contaminación.
Contacta con nosotros
- Detección no destructiva de características internas micrométricas en sistemas microelectrónicos de EEE. - 3rd enero 2022
- Inspección acústica de sistemas híbridos en sustratos laminados - 3rd enero 2022
- Entrada de agua a través de piezas delaminadas en sistemas encapsulados de plástico - 3rd enero 2022